STEAM HUMIDIFICATION UNITS
Proven technic, perfect performance
We are able to design steam humidification units depending on your product spectrum and process details. Moisturizing paper and fabrics by steam is a proven application for decades. Even it’s a well-known proven technic, there are several minute details should be taken into consideration during the system design stage.
Depending on the process details given by the end users, we design the system with fluid dynamics and steam systems’ major rules and formulas. Some design headlines listed here-below;
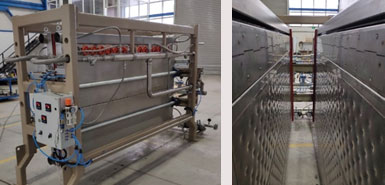 Main carrier frame
Steam distribution network
Steam flow control valves
Steam spray head and orifices
Heating plates
Condensate drainage system and steam traps
Stainless steel frames and pipe-work
Pneumatic and electric control systems
After an engineered design done by our team and approval of the layout drawings by the end user, we start to manufacture the complete system in our workshop.
In order to design a proper steam humidification unit, there are some information should be supplied by our customers. Some main information is listed below. We collect additional information during our site visits and plant audits.
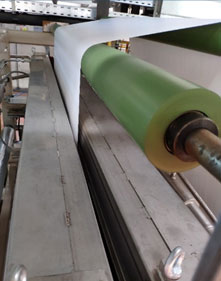 Product details
Max. product weight (kg/m2)
Relative humidity prior to the humidification unit
Targeted humidity levels
Max. speed of your main machine
Min. and max width of your product spectrum
Single or double sided spray
Steam system information (if there is any steam source available)
Available space that the unit would be installed
To secure the system performance there are supplementary processes have to be properly controlled. These are;
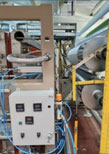 Drying process and accurate temperature control
Cooling/chilled water process
Steam supply chain
Condensate removal
Relative humidity of the manufacturing place
Automation
Poor quality on drier control and fluctuations of the temperatures at the product cut-awayhave negative effect on moisturizing back the process media.
Cooling cylinders should work properly. Cooling system capacity has to cover required heat load. Process media has to be cooled down before and after the steam humidification unit.
Dry and clean industrial steam has to be supplied to the system.
Any condensate trapped inside piping and/or boiler water carried over with the steam
causes quality problems, even manufacturing lost.
Water hammer should defect valves and ancillaries.
Solids carried by boiler water should block heating plates, orifices,
strainers, steam traps, hoses and small holes. They should also stick on
the process media and cause quality problems.
A proper condensate drainage system is essential to have a satisfied operation.
Improper steam trapping should extend start-up period and should cause water
hammer. Condensate flooded inside the heating plates would reduce heat transfer
rate which would have negative effect on humidification efficiency.
Steam flowrate should be controlled manually or digitally. Best optimistic control option
should be decided. Travel of steam flow rate control valve’s trim should be controlled by
a basic PID or driven by the main machine’s PLC system depending on the machine speed.
Inline humidity measurement sensors should be added to the system to provide accurate
steam flow rate. Sophisticated control options increase the investment costs. On the other
hand, automation options bring advantages to eliminate labour mistakes and provide stability.
Relative humidity of the manufacturing and storage halls is an another parameter
to be controlled for a satisfactory operation. During the coating process, temperature
of the plant air tends to increase. This cause relative humidity to decrease.
Low relative humidity of the working and storage environments should create
quality problems at the final product. Paper should shrink, curl and/or loose
dimensional stability.
Working environment air has to recover its relative humidity by water or steam injection to the ambient. Provision of some amount of fresh air to the working environment should also help to improve productivity and to have healthy ambient. Recommended humidity level for working environment is around 55%rh.
Benefits of PienPro Humidifiers;
Fully symmetric design
In case of need you can use each of spraying frames at both sides.
Stainless steel frame work
All of the wet metal construction where steam distribution, spraying and condensation takes place are made of stainless steel to obtain trouble free, long term service life.
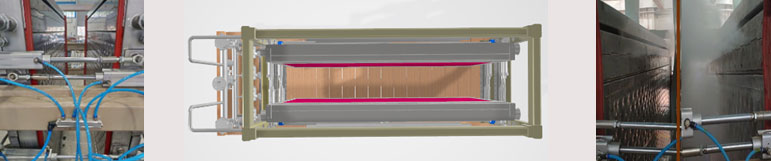
Special heat exchanger at the steam supply
We designed a special pipe in pipe heat exchanger to provide dry saturated steam to the steam spray chamber.
Steam header with compact steam trap and air vent
We equipped our unit with a steam header including a condensate removal pocket and a compact steam trap. There is also an air vent fitted to remove air and non-condensable gasses in the steam space.
Vacuum breakers to secure system under vacuum conditions
At the end of a routine production step, after closing the steam supply to the unit, steam inside the frame condenses because of the radiation losses. This triggers a vacuum. In such cases, vacuum deforms heating plates, steam distribution hoses or any other sensitive ancillary. Vacuum breakers eliminate such deformations.
Special spray chamber with spring loaded variable area
Steam has to be sprayed equally throughout the process media. If not, re-moisturizing performance should not be the same at the media cut-away. We design and manufacture the spray orifices ourselves. Zone control is very easy with spring loaded area control.
Dead space drainage to eliminate water splash
At the beginning of steam spraying, some amount of residual water should splash over the process media and should damage it. We designed dead space drainage system to eliminate such an undesired operation.
Spray zone control
You can control the spray zone depending on the media width. Standard zone control should be done by manual wheels provided on the skid. Automatic control is an option that we can provide.

Perfect control of steam flow rate
We size and select the best suitable control valves to precisely arrange the steam flow rate. Since we supply our control valves with SMART positioners, you can run the valves from your DCS available. Standard input signal to positioners is 4-20 mA. An option for 0/10 V is possible.
All in one steam trap modulesfor perfect condensate removal
Condensate removal is very important for a satisfactory operation. By means of compact steam traps and a perfect mechanical design of the system, condensate removal is very easy and fast. Warm-up period is very short compared with the traditional steam traps. They have a very small foot-print and allow us to make maintenance without stopping the production.
Compact design of the skid to fit in very tight spaces
Mechanical design of the steel/stainless steel frame work carried out in accordance with your available space in the plant. We can design a unit where the clean width is only 1(one) meter and clear height is just 2(two) meters. Length of the unit depends on the maximum width of the process media. Approximately the frame length is 1 meter longer than your maximum product width.(Excluding steam header and steam trap set)
|
|